Structural Analysis - GT Cockpit
- timmorleyracing
- Feb 2, 2021
- 1 min read
Updated: Apr 27, 2022
In motorsport, performance is everything. The Effect Simulations GT Cockpit has been designed with ultimate strength and rigidity at the focus. This ensures perfect transmission of the drivers inputs, and the response of the peripherals to the driver.
Each element and component of the cockpit has undergone an intensive design process, 3D stress modelling in CAD, prototype stage, and eventually into production.
Brake Pressure - Performance Testing
The below image shows the cockpit undergoing a brake pressure test of 85kg, while simultaneously taking 25NM of torque from a Direct Drive wheel base. The study shows a maximum deformation of 0.67mm throughout the cockpit during a 1 million usage cycle test.

Carbon Fibre - Strain Test
The below image shows a strain test on each piece of carbon fibre tube when undergoing maximum loading of 150kg driver weight, 85kg brake pressure and 25nm of torque from the steering input.
Each piece of carbon fibre tube is connected via a CAD designed & optimised component, printed using the latest technologies using PETG material.
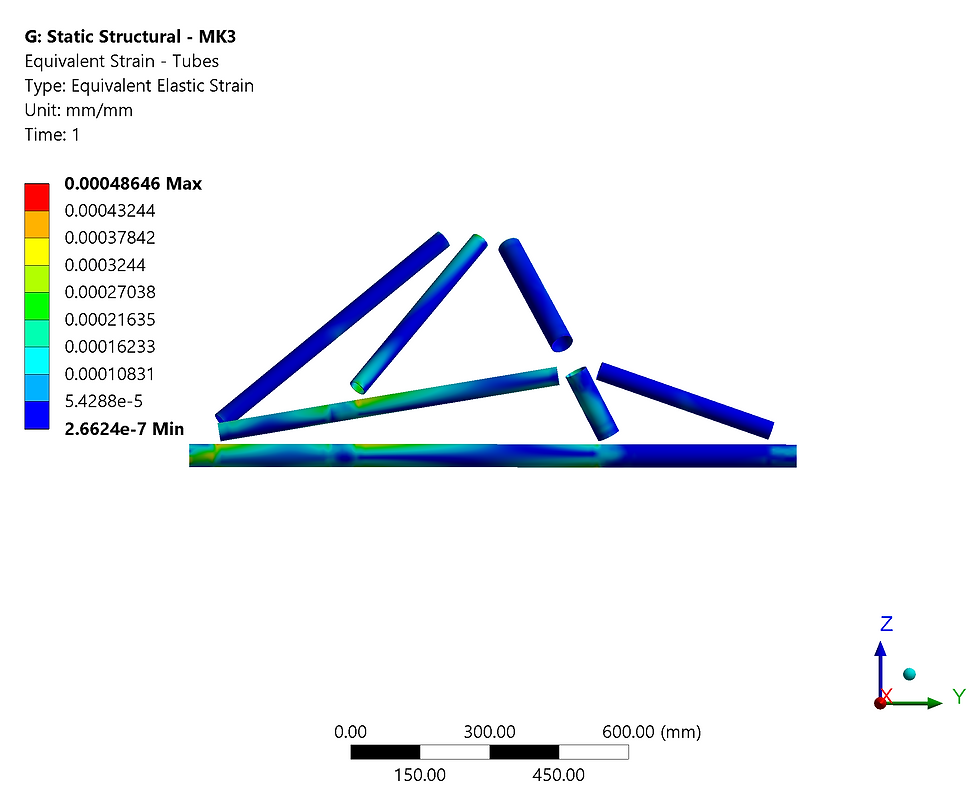
3D Printed Components - Elastic Strain Test
The below image shows an elastic strain test on each 3D printed component tube when undergoing maximum loading of 150kg driver weight, 85kg brake pressure and 25nm of torque from the steering input. It is possible to see a maximum elastic strain of 0.0004mm in some areas of the design. Each component has been subjected to a 1 million usage cycle test using CAD software.

Comments